A. INFORMATION AND PROCEDURE OF MARKING
ISPM 15 is the 'International Standards for Phytosanitary Measures Publication No. 15: Guidelines for Regulating Wood Packaging Material (WPM) in International Trade'.
-
ISPM 15 was developed to address the global spread of timber pests by regulating the movement of timber packing and dunnage in international trade. ISPM 15 describes phytosanitary measures to reduce the risk of introduction and/or spread of quarantine pests associated with solid timber packing material (includes dunnage).
-
ISPM 15 applies to coniferous (softwood) and non-coniferous (hardwood) raw wood packaging material. The standard does not apply to wood packaging made wholly of wood-based products such as plywood and veneer, reconstituted wood products (particle board, chipboard, oriented strand board, high density fiber board, and medium density fiber board) or products created using glue, heat and pressure or a combination of these.
-
Timber packing to be free of bark because bark has the potential to contain numerous pathogens of quarantine concern. It also acts as a shelter site for insect pests and encourages post-treatment infestation by both insect and pathogen pests. The presence of bark also hampers inspection procedures and may reduce the effectiveness of methyl bromide fumigation.
-
Timber packing and dunnage bearing the mark below is certified as having been subjected to an ISPM 15 approved treatment.
ISPM 15 Mark:
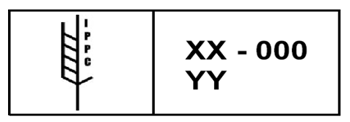
-
ISPM 15 compliant mark must include:
-
IPPC certification symbol.
-
XX: represents the two letter ISO country code (e.g. MYfor Malaysia)
-
000: represents the accredited code number issued by DOA to the treatment provider or wood packaging manufacturer. Inclusion of this certification number ensures that the wood packaging material can be traced back to the treatment provider and/or manufacturer. (e.g. (B) 0123 for Afford Management & Services Sdn Bhd Code)
-
YY: is the treatment abbreviation where:
* HT is the code for heat treatment OR;
MB is the code for methyl bromide fumigation.
-
To aid in validation inspections, ISPM 15 compliant marks should be clearly visible and DOA recommends that they appear on at least two opposite sides of the article being certified. To be ISPM 15 compliant only one mark is required.
-
The marks must be permanent and not transferable. Hence metal plates and stickers are not acceptable
-
The PQ9 / WPM 1 Form have to submit to DOA 48 hours before fumigation date required.
-
DOA will issue the reference control number, wherein this number have to chop below (if possible) or beside on the ISPM 15 mark onto WPM.
-
ISPM 15 mark will be applied onto the WPM before stuffing container.
B. SITE REQUIREMENT
The fumigation site must;
-
Be able to be isolated from unprotected personnel.
-
The distance at least 12 meters from the attaches the building.
-
A ‘risk area’ must be set up with a minimum of 3 meters clearance around the sheeted fumigation enclosure in the open, or
-
6 meters clearance in an enclosed area
-
Be well ventilated.
-
Be sheltered from high winds and raining (as much as possible, especially for LCL Fumigation)
-
Have a smooth gas impervious floor (see B.2. Site floor)
-
Have a power supply available.
B.1 Site floor
-
The fumigation site floor must be impermeable to the fumigant if fumigation under gas proof sheets is to be carried out.
-
The floor of any site used for sheet fumigation must be;
-
Flat and free of stones and other sharp objects so that a gas-tight seal can be made between the sheets and the floor;
-
Free of cracks (including unsealed expansion joint in concrete floors) and drains or any other openings that will reduce the gas-tightness of the enclosure.
-
Where unsealed cracks or drains are present, they must be no closer than 1 meter from the fumigation enclosure.
-
Surface sealed with concrete or hot mix asphalt, that is, with a smooth surface finish that are in good condition and meet the requirements listed to the left, generally provide good floor surface for effective fumigation.
-
Surfaces such as soil (including cement consolidated soil), sand, base rock and paving (stones or blocks) do not provide a suitable floor for a fumigation enclosure.
-
On porous or unsuitable surfaces, floor sheets should be used for sheet fumigation;
-
Gas proof sheets should be used or the floor should be permanently sealed;
-
Plastic sheeting or paper containing a tar (asphalt) layer may be used for this purpose.
C. FREE AIR SPACE & IMPERVIOUS WRAPPING SURFACE AND COATINGS
A minimum total of 350mm free air space must exist above, below and around the commodity in shipping containers to allow for effective circulation of the fumigant.
-
Free air space must also exist between dense commodity components such as timber.
- Individual planks, rounds or articles have at least one physical dimension which is less than 200mm (8 inches) thick;
-The commodity is separated by a minimum of 5mm in one dimension every 200mm (8 inches);
-There is adequate physical distance, at least 50mm (2 inches) between the timber and the base and sides of the fumigation enclosure.
* Methyl bromide will only penetrate 100mm (4 inches) from the surface into the timber
within the fumigation exposure period. Because of this, it is important to use separators to
ensure effective circulation of methyl bromide around and throughout the commodity.
Commodities that are to be fumigated must not be wrapped, painted or coated in materials impervious to the fumigant.
Commodities which may contain quarantine pests and which are covered with or packaged in ‘gas impervious materials’ (materials that the gas cannot pass through) such as plastic wrapping or laminated plastic films, aluminum foil, tarred or waxed paper, must have the impervious material opened, cut perforated or removed prior to fumigation. This must be sufficient to allow both adequate gas penetration into the commodities and effective ventilation (airing).
Gas impervious materials (plastic wraps, cellophane, film, shrink wrap, aluminum foil and papers that are tarred or waxed, laminated, or waterproofed) that meet AQIS perforation requirements do not need to be slashed, opened, cut or removed.
To meet AQIS perforation requirements for fumigation, impervious materials must contain not less than four (4) perforations of 6 mm diameter/100sq cm or five (5) perforations of 5 mm diameter/100 sq. cm. Plastic wraps containing numerous pinholes (at least 6 holes per sq. cm), frequently used for transportation of fruit and vegetables are also acceptable.
D. FULL CONTAINER LOADED (FCL)
The Container must be positioned on the floor.
-
Electrical fan will be used to circulate gas evenly in the fumigated space.
-
Sampling tube will be installed to monitor the gas concentration at the starting and ending point of the exposure period.
-
Fumigation will be carried out under the plastics sheet.
-
Our plastics sheet will enclose the container.
-
The plastics sheet will be sealed to the floor to ensure airtight enclosure and to avoid from gas leakage.
-
The amount of gas released is calculated based on the ‘enclosure’ volume
-
The Methyl Bromide hot gas at a dosage rate of 48 grams/m3 will be contained for the period not less than 24 hours for extermination.
-
After 30 minutes gas release complete, the gas concentration in enclosure would be monitor for ‘Start Point Monitoring’. Wherein, if the all reading for gas concentration at or above the standard requirement and in equilibrium, the fumigation process is consider started for fumigation exposure period. (following the requirement).
-
When the fumigation exposure period is achieved, the gas concentration in enclosure would be monitor for ‘End Point Monitoring’. Wherein, if the all reading for gas concentration at or above the standard requirement, the fumigation process is considered successful and ventilation process can be started.
-
The duration of aeration process depends on the commodity and packaging.
-
The Threshold Limit Value (TLV) should be monitor for the safety requirement. If, the TLV reading is 5ppm and below, the enclosure is considered safe to re-enter.
E. LESS CONTAINER LOADED (LCL) / STACK FUMIGATION
-
The cargo must be positioned on the floor.
-
The place must be sheltered from high winds and raining
-
Frame will be used to ensure gas circulation evenly in the fumigated space.
-
Electrical fan will be used to circulate gas evenly in the fumigated space.
-
Sampling tube will be installed to monitor the gas concentration at the starting and ending point of the exposure period.
-
Our plastic sheet will enclose the cargo. The plastic will be sealed to the cemented floor to ensure airtight enclosure and no gas leakage.
-
Fumigation will be carried out under the plastics sheet.
-
The plastics sheet will be sealed to the floor to ensure airtight enclosure and to avoid from gas leakage.
-
The amount of gas released is calculated based on the ‘enclosure’ volume
-
The Methyl Bromide hot gas at a dosage rate of 48 grams/m3 will be contained for the period not less than 24 hours for extermination.
-
After 30 minutes gas release complete, the gas concentration in enclosure would be monitor for ‘Start Point Monitoring’. Wherein, if the all reading for gas concentration at or above the standard requirement and in equilibrium, the fumigation process is consider started for fumigation exposure period. (following the requirement).
-
When the fumigation exposure period is achieved, the gas concentration in enclosure would be monitor for ‘End Point Monitoring’. Wherein, if the all reading for gas concentration at or above the standard requirement, the fumigation process is considered successful and ventilation process can be started.
-
The duration of aeration process depends on the commodity and packaging.
-
The Threshold Limit Value (TLV) should be monitor for the safety requirement. If, the TLV reading is 5ppm and below, the enclosure is considered safe to re-enter.
F. CHAMBER FUMIGATION - VAPORMATE TREATMENT
The Container must be positioned on the floor.
-
Electrical fan will be used to circulate gas evenly in the fumigated space.
-
Sampling tube will be installed to monitor the gas concentration at the starting and ending point of the exposure period.
-
The amount of gas released is calculated based on the container volume
-
The VAPORMATE hot gas at a dosage rate of 290grams/m3 will be contained for the period not less than 4 hours for extermination.
-
After 30 minutes gas release complete, the gas concentration in container would be monitor for ‘Start Point Monitoring’. Wherein, if the all reading for gas concentration must be at or above the standard requirement and in equilibrium.
-
When the fumigation exposure period is achieved, the gas concentration in enclosure would be monitor for ‘End Point Monitoring’. Wherein, if the all reading for gas concentration at or above the standard requirement, the fumigation process is consider successful and ventilation process can be started.
-
The duration of aeration process depends on the commodity and packaging.
-
The Threshold Limit Value (TLV) should be monitor for the safety requirement. If, the TLV reading is100ppm and below, the enclosure is consider safe to re-enter.
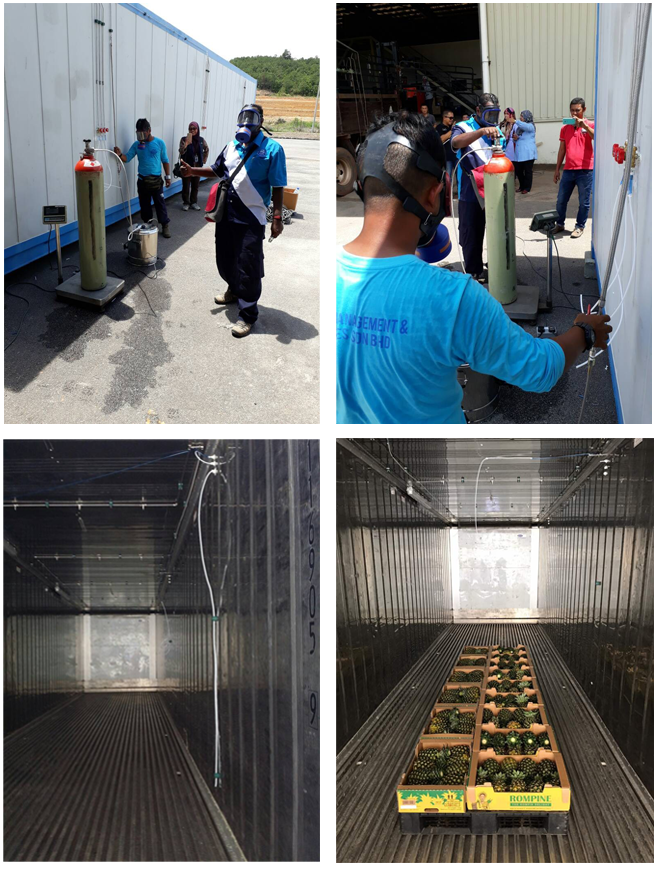